Optical measuring and testing systems for production inspection
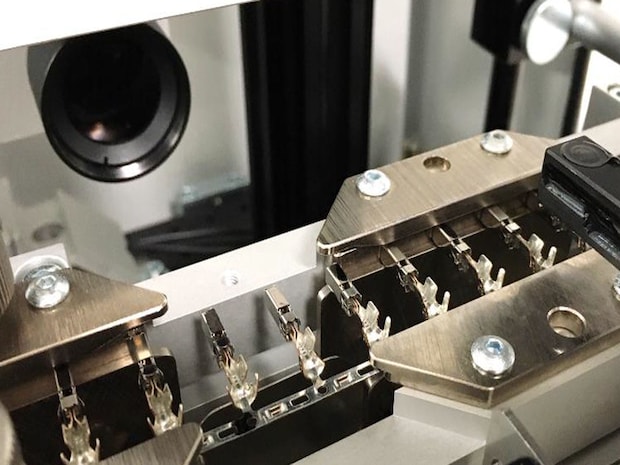
In-Line testing of connectors
Jenoptik manufactures optical measuring and inspection systems based on industrial image processing. Since September 2018, this business has been strengthened by OTTO Vision, a partner for high-end applications in industrial image processing with a focus on optical 2D and 3D inspection systems for product control as well as complex image processing systems for application in parts inspection, surface inspection and position recognition.
The ideal industrial and scientific environment as well as the outstanding qualification of the employees are a guarantee for innovative top technologies. Today Jenoptik supplies tailor-made products with a wide range of services to solve complex inspection tasks. Customers in Europe, Asia and America trust these technologies.
OTTO Vision Technology GmbH was transferred to JENOPTIK Optical Systems GmbH by means of a merger through inclusion and took effect on September 30, 2021 with the entry in the relevant commercial registers. The business of OTTO Vision Technology GmbH has since been continued in JENOPTIK Optical Systems GmbH.
Our product fields at a glance
Optical inspection stamping
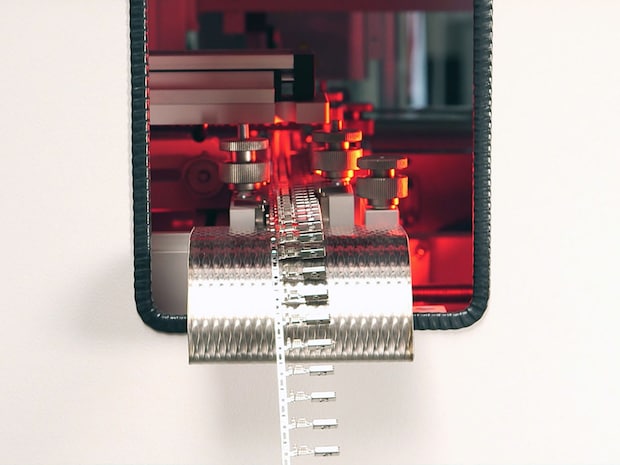
optical inspection stamping parts
Test station for 100% inspection of punched strips and punched parts.
Vision systems and software
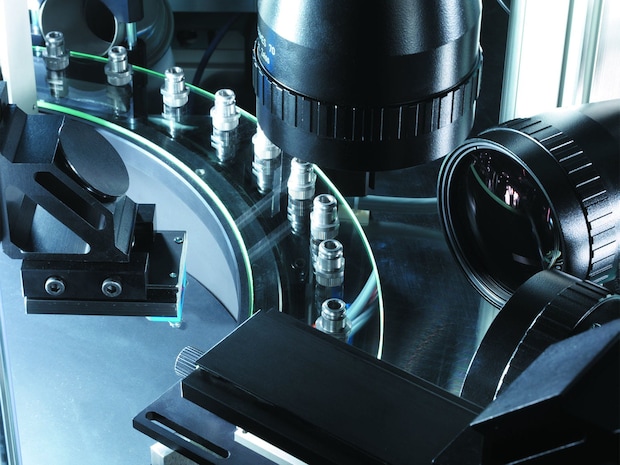
Customer specific sorting machines and vision systems
Vision software for high precision part measurement and surface inspection.
Our industries
Automotive and supplier industry - 100% inspection and sampling of serial parts and prototypes during production
Especially in the automotive industry and its suppliers, there is a broad demand for camera-based automation solutions in order to design manufacturing processes effectively and to ensure a high level of quality. Our vision systems are therefore used in automatic assembly machines, in inspection and sorting systems for 100% inspection of components as well as in optical inspection stations for spot checks of individual parts or prototypes. Typical test objects are small parts of any kind, but also larger components such as drive shafts, axle journals, forged parts and many others.
Transmission parts
- Inspection of forging blanks 2D and 2 1/2D geometry inspection with image processing and laser light-section methods
- Check for sufficient material for the follow-up process
Kingpin
- Sorting plant for axle journals
- Sorting of different types based on the recognition of geometric features
- thread check on journal
- Contour accuracy test
Drive shafts
- 100% inspection of drive shafts in the CNC machining centre
- Testing of varietal purity, correct position and loading
- End measurement of the manufactured shaft
- Data feedback to CNC control
Sleeves
- 100% testing of cylindrical components (sleeves)
- Diameter, ovality and gap dimension of the sleeves
- Detection of lint on edges and surfaces
- Guarantee of varietal purity
Aerospace industry - Providing highly accurate 3D data for optimization and production monitoring of turbine blades
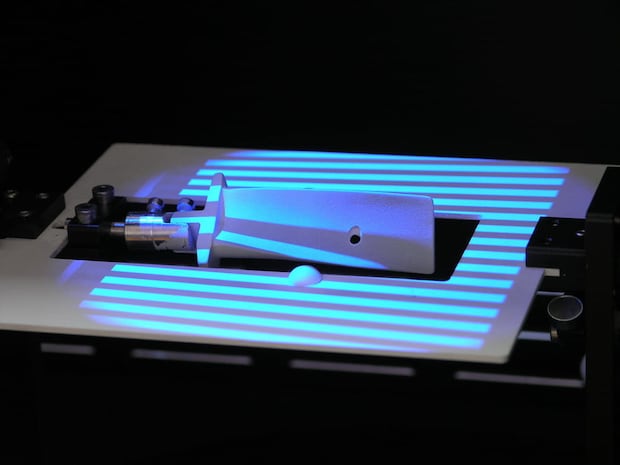
Turbine Blade
The provision of highly accurate 3D data of turbine blades is of particular interest to the aerospace industry. The data are used for simulation and optimization as well as for initial sample and production control of machined or additive manufactured or coated serial components. In addition, optical 3D measuring systems provide information on wear and tear and thus on the optimal reworking of used components by laser cladding during maintenance.
Mechanical and plant engineering - integration of vision systems and automation solutions
As a partner for the specialists in mechanical and plant engineering, we provide with our own vision systems measuring and testing solutions for the integration and completion of customer-specific individual projects and series machines. The extensive software libraries and diverse software interfaces allow even complex, interlinked automation solutions to be realized. With the tools of artificial intelligence, additional test engineering requirements can be met today that were unsolvable with standard methods of 2D and 3D image processing.
Automatic punching and bending machine
- 100% control of punched and bent parts in automatic machines
- Precise contour inspection during the manufacturing process
- Use of several high-resolution cameras for visualization and precise measurement of large components
2-spindle drilling machine
- Post-etch 2-spindle drilling machine for printed circuit boards
- Automatic alignment with two-camera image processing
- Motor control with three motors
- Total accuracy per layer 1-2 µm
Medical technology - Testing of implants and prostheses
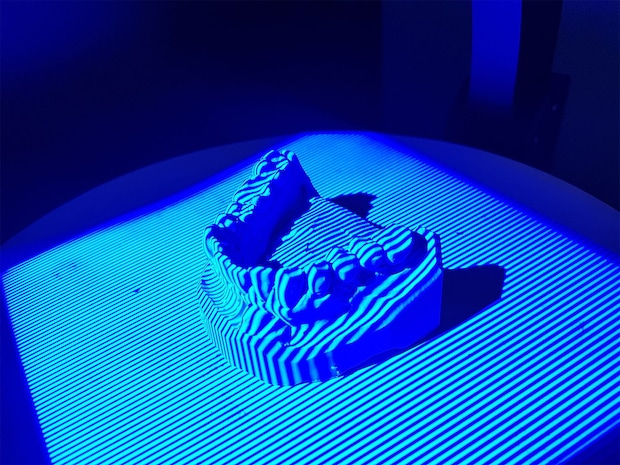
Inspection of dentures
Metalworking industry - Quality inspection and process control for tool components and small parts
A camera system does not differentiate between a plastic, glass or metal part: The optimal solution is determined by the interaction between optics, illumination, camera technology and of course the software of a vision system. Nevertheless, the metal processing industry is of particular importance - due to the number of pieces produced, the high quality standards and the resulting inspection requirements. With our vision systems we inspect deep-drawn parts as well as turned parts, sintered and cast parts, piston rings, tool parts and many others.
Piston rings
- 100% inspection of the surface of piston rings
- All-around inspection during part rotation
- Defect detection with high resolution on the top and bottom side of the part as well as along the inner and outer surfaces
- Component diameter from 30 - 120 mm
Thermoformed sleeves
100% inspection of thermoforming sleeves in an automatic rotary indexing machine
Part inspection during 360° rotation
Detection of cracks and surface defects
Testing of approx. 50 parts per minute
Turned part inspection
- Combined inspection of turned parts for surface defects and geometric features
- Downstream sorting based on the test results
- Optionally clocked or continuous part throughput
Mold cores for injection molds
- Inspection of eroded mould cores as part of the incoming goods inspection
- Planar 3D scanning with fringe projection
- Automated part handling with reference turning fixture
- Automated target-performance comparison to CAD
Sintered metal parts
- 100% inspection of sintered metal parts
- Detection of surface defects
- Guarantee of varietal purity
- Throughput approx. 80 parts per minute
Zinc Die Casting
- Initial sampling and prototype measurement of zinc die-cast parts
- Highly accurate, automated data acquisition
- Full area 3D digitization with fringe projection
- target-performance comparison to CAD data
- Determination of form and position tolerances
Hose clamps
- 100% testing of hose clamps
- Geometry inspection from two views
- Varietal purity
- Up to 300 parts per minute
- Feeding with storage hopper and vibratory conveyor
Screws
- 100% inspection of screws
- Multi-camera system
- Screws hanging in the flow
- Eddy current crack testing
- Mechanical testing of the internal drives
Plastics processing industry - Production monitoring of moulded parts, hybrid parts and assemblies
Inspection systems from OTTO Vision are successfully used in various areas of the value chain in the plastics processing industry. First samples, prototypes and random samples can be holistically evaluated with optical 3D measuring systems and compared against CAD target models. In addition, molded and hybrid parts as well as overmolded strip products are 100% inspected for dimensions, completeness and presence of details as well as for overmolding or material residues. Our vision systems are therefore widely used in automatic assembly machines, inspection stations and measuring systems.
Hybrid parts
- 100% inspection of overmoulded metal parts (multicoloured)
- 6-camera system
- Arrangement directly after injection moulding machine
- Check for dimension, completeness, overspray etc.
Moulded parts
- Initial sampling and prototype measurement of plastic injection moulded parts
- Highly accurate, automated data acquisition
- Full area 3D digitization with fringe projection
- Target-performance comparison to CAD data
- Determination of form and position tolerances
Plastic circuit boards
- Monitoring of injection moulds through random sampling
- Contour accuracy of the parts
- Testing of protruding nipples for presence and length
- 16 tests possible per shift
Plastic gaskets
- 100% inspection of plastic seals in the punching tool
- Parallel operation of two in-die modules in one mould
- Control for parts separation
- Inspection of geometric features and for surface defects
Stamping technology - Testing of punched strips and loose falling parts in the tool, after the tool and in the electroplating
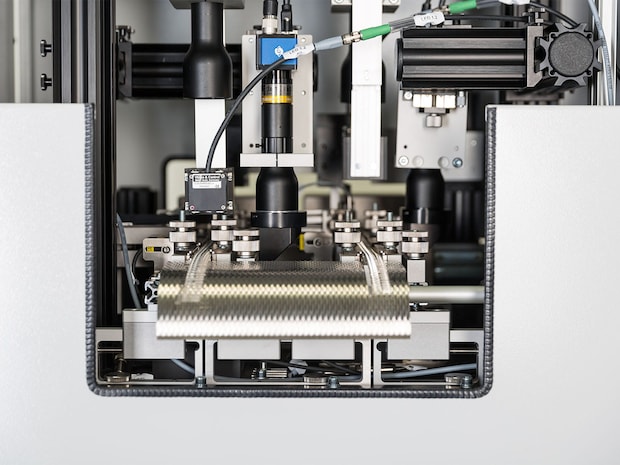
PSS-40 Double Track
Every day, billions of stampings are produced worldwide as loosely falling products and as strip products in progressive dies, on automatic stamping and bending machines or in transfer presses. The output can amount to several thousand parts per minute, production tolerances are now in the small hundredths of a millimeter range. In addition to the demand for 100% control, the customer expects high system availability, efficient changeover processes, material savings, traceability and continuous cost reduction. As the technology leader in this segment, Jenoptik offers OTTO Vision solutions for quality control and process monitoring for the stamping and forming industry and electroplating with complete inspection stations for strip products as well as with customized vision systems.
Connectors
- 100% inspection of connectors
- Parts testing on all presses with the test stations of the PSS-40 device family
- Inspection of geometric features, contours, weld spots and surface defects
- Immediate detection of missing parts, tool inspection and process optimization
Male connectors
- 100% inspection of male connectors
- Parts testing on all presses
- Use of test stations with up to 6 cameras
- Inspection of geometric features and contours
- Operation and data archiving via a central control station
Press-Fit Contacts
- Fast, non-destructive inspection of the press-fit zone of press-fit contacts
- High-precision, extremely high-resolution 3D digitization with stereo sensor
- Fully automated data acquisition and evaluation
- Suitable for workers and production
- Replacement of time-consuming, manually created micrographs
- Sampling
- Measuring time approx. 5 min
Punched grids
- 100% control of punching grids
- Test cells with up to 8 cameras
- Inspection of geometry and contour features
- Testing of up to 300 characteristics per article
Razor Blades
- 100% control of blades in the punching tool
- 500 Stroke double falling, per stroke 120 Test parameters
- Control for parts separation
- Inspection of geometric features and weld spots
Seal inspection in the tool
- 100% inspection of seals in the punching tool
- Parallel operation of two in-die modules in one mould
- Control for parts separation
- Inspection of geometric features and for surface defect points
The business segment OTTO Vision of the Jenoptik Group
About Us
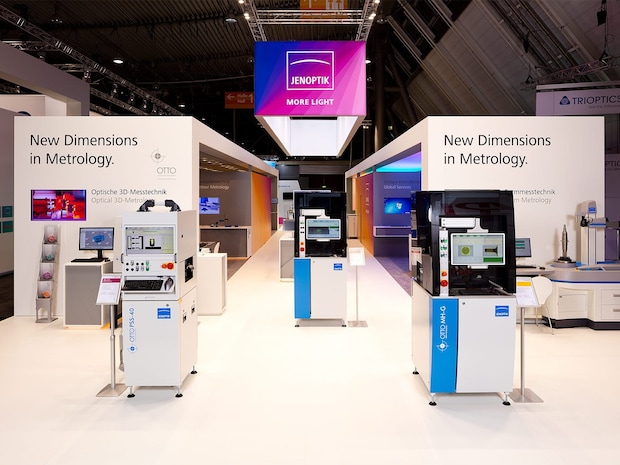
For 30 years now, Otto Vision inspetion systems have stood for high-end machine vision applications in the supplier, automotive, stamping and glass industries as well as many other sectors of the global market.
OTTO Vision Technology GmbH - we maintain a close cooperation with partners in precision optics, mechanical engineering and image processing hardware. On this basis we develop complex inspection and sorting systems as well as sophisticated measuring systems, which are now used in approx. 2,000 industrial applications.
OTTO Vision Technology GmbH - we rely on the trustful cooperation with our customers and consider it a decisive basis to combine industry-specific requirements and metrological services.
Technologies for your production
"We combine team spirit with creative individual performance in order to find the optimal solution for every testing task. Dr.-Ing. Dr. rer. nat. Roland Fiedler
OTTO offers its customers integrated technologies for product control and process optimisation. The inspection systems are based on a uniform hardware, software and control concept. They are part of a test system and data management (PSDM). This unit of precise testing and intelligent data evaluation enables an analysis and optimisation of the production processes beyond quality assurance.
OTTO vision technologies lead to multiple customer benefits: 100% inspected parts, shorter start-up phases, longer machine runtimes, less material consumption, more continuous production, reduced effort for inspection during production, minimization of complaints, better user satisfaction and competitiveness...
Everything from one source
The success of OTTO Vision Technology is based on its comprehensive expertise in the areas of software development, design and production. With this potential, the functionality of the devices is guaranteed in the long term and the technology is kept up to date.The continuous customer support from technical advice to professional project realization and service is provided by the company headquarters as well as by the regional sales and service offices.
Milestones in business development
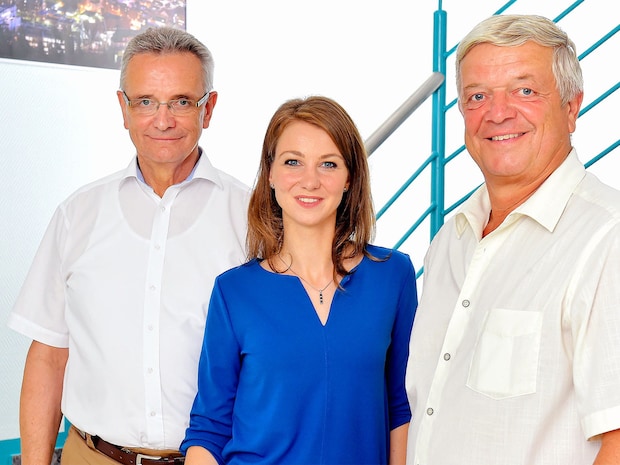
Kristin Holzhey and the founder Gunter and Reinhard Otto
- 2021: Fusion of Otto Vision Technology GmbH with JENOPTIK Optical Systems GmbH
- 2019: OTTO Vision wins the Jenoptik Group's Innovation Award with the FLEX-3A 3D scanner
- 2019: Kristin Holzhey takes over the management
- 2019: Market launch of 3D scanners with high-resolution 12-MP cameras
- 2018: 100% takeover by the JENOPTIK Group
- 2016: BRUDERER MACHINERY (SUZHOU) LTD. takes over representation in China
- 2015: Extension of the company building
- 2013: First projects in China and Brazil
- 2012: New generation high-speed image processing
- 2010: Expansion of business activities into the field of optical 3D metrology
- 2008: The 1.000th system was installed
- 2004: BRUDERER MACHINERY INC. takes over the representation in the USA
- 2002: Market launch of test stations for punched strips, sorting machines and measuring robots
- 2000: moved into own company building in Jena-Maua
- 1997: Development of a new device generation for the container glass industry - a testing device for online inspection of still glowing glass containers
- 1995: First major project in the automotive industry - a complex testing and sorting system for Ford-Werke AG
- 1994: First applications in the high-performance stamping industry and in mechanical engineering
- 1993: Development of an own image processing system CVS 100
- 1992: Company foundation by Gunter and Reinhard Otto as an engineering office for industrial image processing
Do you have any questions?
We will gladly advise you.
+49 3641 67-1515