RecommendMail Facebook LinkedIn
- Industry 4.0
Laser drilling in plastics – with reproducible precision
Within just six months, the machine builder Contexo, specialist for high-performance systems, and the photonics expert Jenoptik successfully developed a laser drilling machine for an innovative plastic product. Both partners bundled their experience in the area of customized automation solutions and integrated subsystems for laser applications.
, Steffen ReinlLaser technologies are becoming increasingly important for achieving even more precise processing results at lower costs and higher productivity. They frequently expand the application limits of conventional processing techniques such as micro-drilling.
Often the objective for machine builders is to supplement the existing core expertise in the areas of machine design, machine control and component handling with innovative optical and laser technologies. It costs time and money for a machine building company to develop the required expertise.Jenoptik offers a solution approach tailor-made for machine building
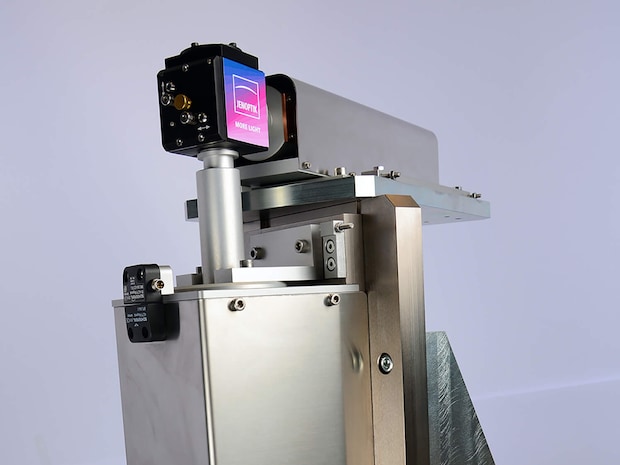
Thanks to easy integrable optical system platforms such as JENvelt™, Jenoptik enables manufacturers of laser production systems to integrate the necessary technology as a subsystem. At a competitive cost and in less time, Jenoptik’s application requirements can thus be quickly translated into “optics” and “laser technology”. From a less complex design to a smart and camera-based unit with image processing. The result is a solution that contains all the necessary components and can be integrated into a machine. The basis for the rapid implementation is a platform concept of tried-and-tested components for guiding, shaping and moving the laser beam, image processing components and software.
An OEM project such as this was created from the collaboration of the Jenoptik team and the machine builders Contexo: an opto-electronic assembly with image processing for laser drilling an innovative plastic product. It was to be designed and manufactured for integration into a laser production system for a customer in the food industry.The challenge – micro-drilling with a consistent hole size
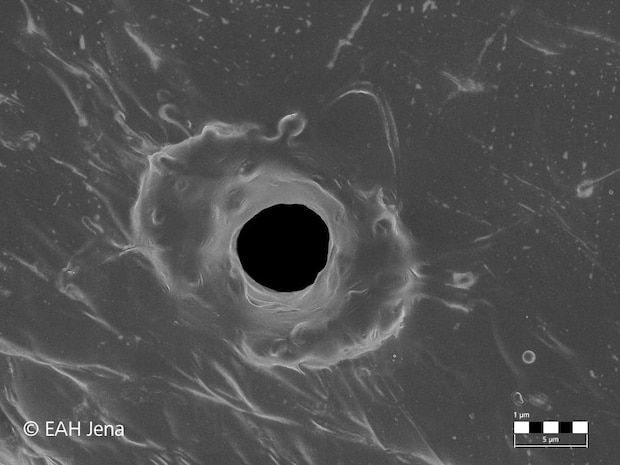
There are very many applications in the food industry that require the creation of micro-holes in thin plastic materials. It is used, for example, for controlled release of moisture through food packaging; on the one hand to prevent it from drying out too quickly and, on the other, to prevent mould developing. Another application is the provision of a defined nozzle opening. In this case, the requirement was to “laser drill” small holes microscopically with a diameter of 6 micrometres in 0.1 millimetre thin plastic, 30 times per minute, with a tolerance of less than 5 percent. For comparison: a human hair has a diameter of around 50 micrometres!
Conventional processing methods, such as mechanical micro-drilling or micro-stamping, have the disadvantage that the reproducibility of hole geometry and size cannot be guaranteed and it is not possible to achieve the required small hole sizes in the micrometer range. “Traditional” laser technologies that use CO² lasers generate too much heat at low material thicknesses, resulting in component deformations in the area of laser processing. For this reason a high-end picosecond laser in the ultraviolet spectral range of 355 nanometres was used.
An important criterion for the design of the optical assembly was to ensure a constant hole size in the workpiece and to tolerate machine vibrations – without any loss of machining precision.Light is the key
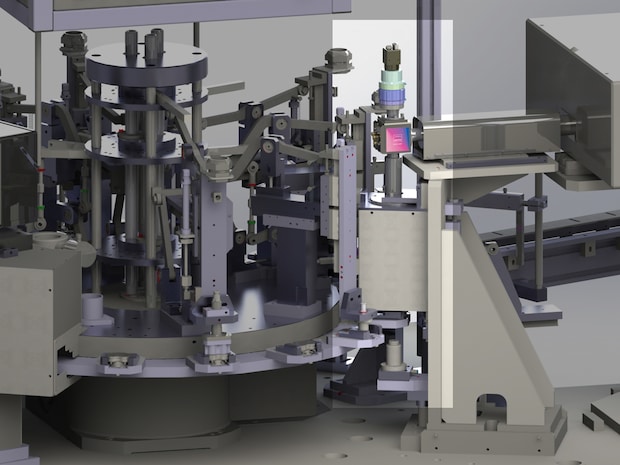
As a development and production partner for optical OEM solutions, Jenoptik can draw on their wide-ranging expertise and technologies, which is what it did in this project – from optics design through image processing to laser technology.
The Contexo-Jenoptik project team chose this approach because of the requirements for precision and reproducibility: The solution lies in the residual light. This passes through the hole created during the laser drilling process and can be detected, i.e. “measured”, on the rear of the component. The idea was brought to life by Jenoptik with the help of integrated image processing and the corresponding electronics. Data acquired optically is evaluated using software and used to switch off the laser energy at precisely the right moment, thus ensuring a consistent hole diameter with varying material thickness. Steffen Reinl: “We were able to use existing technologies from our company group and only had to make adjustments for this process.”
As a project partner of Contexo, Jenoptik provided a solution package that includes optical components specially suited to the application, works reliably with the selected laser source and contains adapted sensor technology for process control for “micro-drilling in plastic”. Naturally, support was also provided to the project partner when it came to integrating the solution into the machine.
Steffen Reinl, who has been part of the Jenoptik project team from the very beginning: “We developed an OEM module that is easy to integrate. The exact specifications for installation space, laser type, drilling accuracy, as well as the working distance to the workpiece and adjustability in the optical system all had to be mapped. On the one hand, the challenge here was the large aspect ratio of the hole diameter and hole depth and, on the other, ensuring reproducibility.”The project
The project began in August 2018 and was successfully completed in the first quarter of 2019 after just six months of development. The exciting moment of integration into the machine environment came in December 2018. The Jenoptik engineers had already put the optical beam path through its paces in their laboratory. Steffen Reinl: “We didn’t want to leave anything to chance. We received the picosecond laser for the so-called ‘Factory Acceptance Test’ from the design team at our cooperation partner Contexo, which allowed us to carry out practical tests at our Jena site. This is essential as a technical verification of functionality and preliminary acceptance of the optical system prior to installation. Everything ran smoothly and we were able to send the system to our partner Contexo in Winterbach with a very positive feeling.”
Product recommendation
About Steffen Reinl
Steffen Reinl has many years of experience in the fields of industrial laser material processing. In 1997 he obtained a master's degree in general machine engineering from the Darmstadt University of Applied Sciences with the specialization in laser material processing with semiconductor lasers. At JENOPTIK Optical Systems GmbH Steffen Reinl is responsible for the technical advice and sales of the new optical subsystems for laser material processing.