JENvelt® vision-enhanced laser tool
Ready-to-install optics module for accelerated process development and commissioning in laser material processing
The JENvelt® system combines a 2D Galvo Scanner, F-Theta lens and camera with integrated image processing and is rounded off with intelligent software. You will benefit from quicker development times and a smart software solution that guarantees optimitzed time-to-market. As a compact plug & play system, it can be easily integrated into existing systems and takes into account the processing requirements of laser production.
The core of the system is the all-in-one software, which combines scanner and laser control as well as image recognition. It maps production projects, monitors the ongoing process and evaluates and gives feedback to the data collected in the control system. Customers particularly appreciate the following advantages:
Acceleration of process development the through machine-capable “smart black box” concept
- Integration of image processing opens up new possibilities for setting up and optimizing laser processes
- Optical know-how for selecting the optimal components and software algorithms is key. Laser machine manufacturers require ready-to-install solutions from optics specialists such as Jenoptik
- Image processing-based evaluation of the process enables in-process quality control
JENvelt® stands for integration and optical know-how
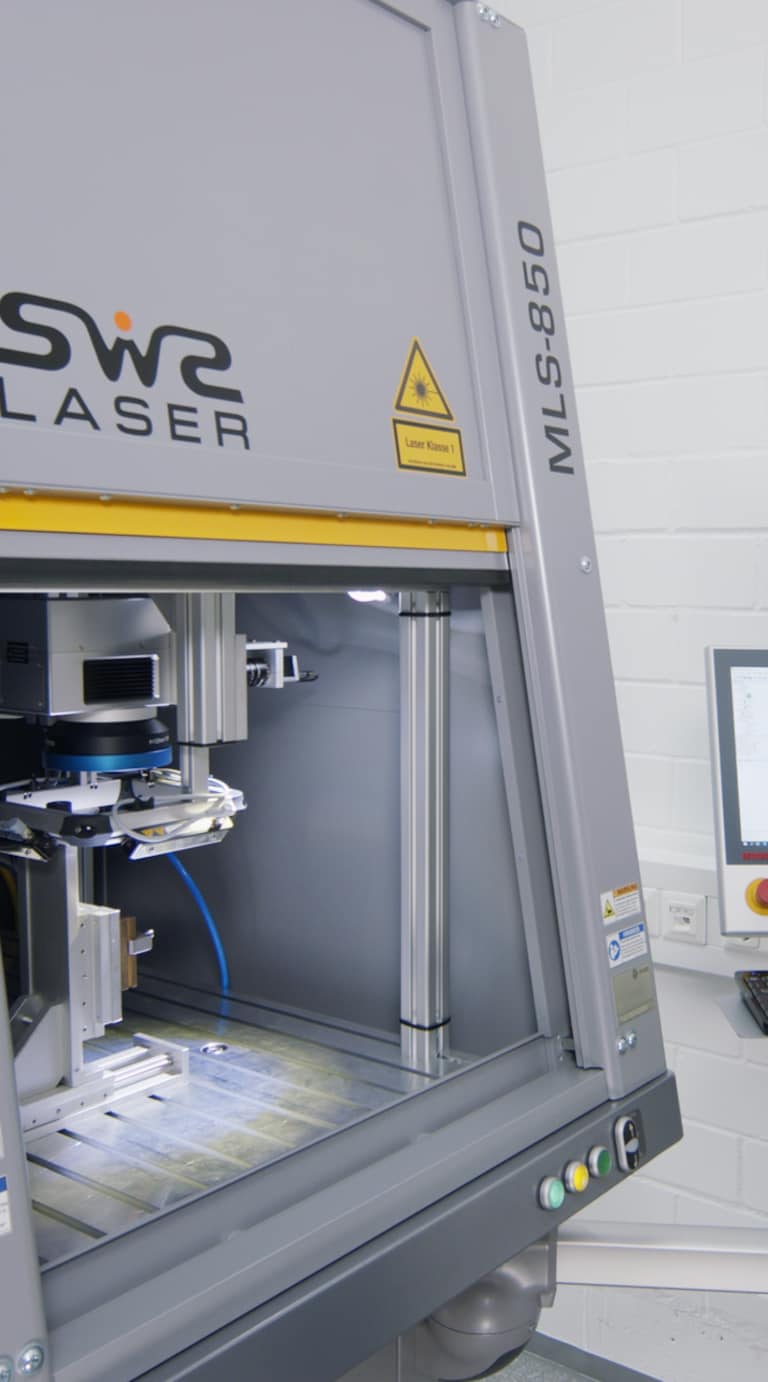
More information
Flexible
Motorized adjustment of spot size supports many applications without changing the optical setup
Ready-to-use
Fully aligned, calibrated and qualified optical system for replicable machine integration
Time saving
Visual setup of the laser process via the imaging channel instead of lengthy, trial-and-error setup
Visualizable
Imaging designed in such a way that, e.g., through laser-transparent material, internal features or components can be examined
All-in-one software
Combines scanner, laser and camera control in one solution for less setup, fewer compatibility issues and improved usability
Accurate
Positioning of the laser using image recognition; position-independent processing thanks to software-based feature recognition
Flexibility with the JENvelt®, no matter the laser application or task
The JENvelt® subsystem is perfect for a wide range of applications in laser material processing. Different laser applications can be carried out with the same optical system in many industries, such as plastics, medical, electronics or automotive. The system components are selected to cover a very wide range of performance parameters. Instead of having to request, procure and commission an individual system configuration for each new application, the parameters can be easily converted to the new system configuration with the JENvelt® optics module once installed.
Typical tasks for which the JENvelt® is particularly suitable due to its accuracy and flexibility are:
- Laser welding of metal and plastic
- Laser cutting
- Laser marking
- Selective laser soldering
- Laser engraving
- Laser cleaning
JENvelt® system hardware
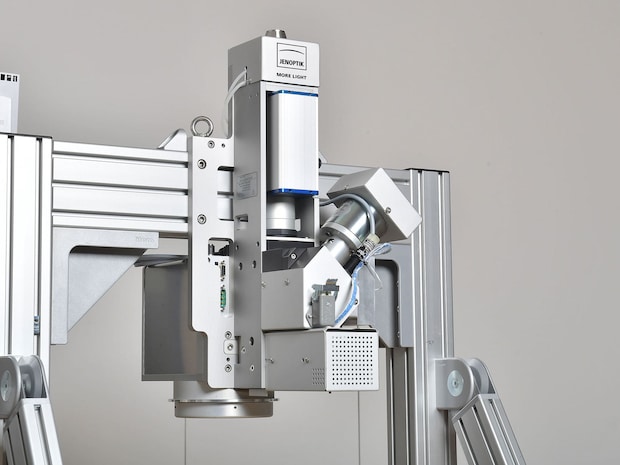
Optical subsystem
- State of the art components
- Adjusted, calibrated and sealed upon delivery
- Machine integration ready
Control unit
Industrial PC: robust and low-maintenance IPC
JENvelt® Software
- Combines scanner control, laser control and image processing
- Simple teach-in
- Position and pattern recognition
Other components
Removable concept laser, workpiece lighting, laser shutters, coolers, etc.
JENvelt® system software
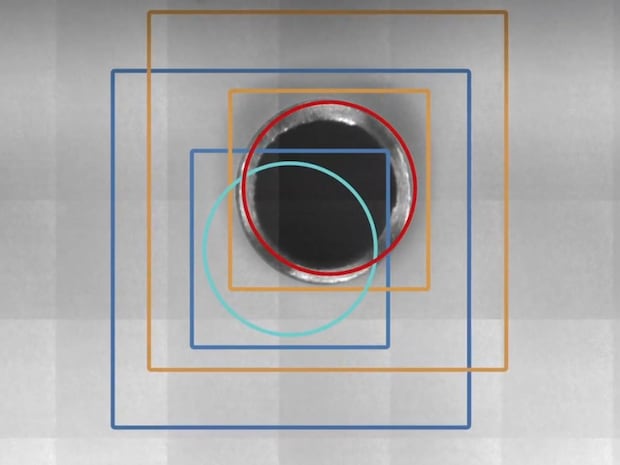
automatic laser pattern correction
The heart of the JENvelt® is its comprehensive software. It is very intuitive to use and user-friendly, which eliminates the need for extensive training of operating personnel after commissioning.
The software package offers a real-time and focused display that allows for easy reading of process-relevant data. In addition, very large amounts of data can be generated. Additonally, the software offers significant advantages in the following areas:
Compensation of tolerances and smart workpiece positioning
The laser path is precisely matched to the position of the workpiece. The JENvelt® repositions the laser spot during running processes if necessary.
Generation of a high-resolution image via stitching
The inline camera takes single shots, which are combined to create a high-resolution overall view of the workpiece. This is the basis for the alignment and orientation of the laser path.
Correction of the laser path using fiducial markers
The software determines the position of the path to be lasered based on reference points and corrects them as necessary. The software detects the reference points on the workpiece regardless of the position and alignment of the component. The software corrects the path to be lasered relative to the detected reference points. Corrections (shape matching) can also be made using the software.
JENvelt® technical data
Optical head
Optical parameter
Optical parameter | ||||
---|---|---|---|---|
Focal length (mm) | 255 | 423 | 635 | |
Working distance | 303.3 | 500.2 | 732.8 | |
Rectangular working field (X x Y) (mm2) | 114 x 114 | 255 x 255 | 500 x 500 | |
Laser class (EN60825) | 4 | |||
Adjustable focus size 1)(mm) | 0.4...1.5 | 0.6...2.4 | 500 X 500 | |
Wave length | 1030...1080 nm | |||
Recommended laser source | Fibercoupled cw laser 100 or 200 µm fiber diameter, NA 0.06 to 0.1 | |||
Fiber coupling | QBH or QBH compatible fibers | |||
Max. laser power (cw) | max 600 W2) | |||
Suitable for pilot beam wavelength | 650 nm |
1) at 100 µm fiber
Mechanical and cooling
Mechanical | Cooling | ||
---|---|---|---|
Outer dimension (mm3) | 400 x 300 x 600 | Water/air cooling | Water/air (depending on laser power) |
Weight | < 25 kg |
Inline camera
Inline camera | |||
---|---|---|---|
Sensor type | Si-CMOS | ||
Resolution | 280 x 1020 pixel2) | ||
Max. field of view in working plane (mm2) | 12 x 12 | 20 x 20 | 32 x 32 |
Frame rate (max. value at full resolution) | 200 fps | ||
Typical exposure time | 10 ms |
2) others upon request
Control interface
Control interface | ||
---|---|---|
Size | 19", 4HU | |
Weight | 10 kg | |
Mains | 100-240 VAC, 50/60 Hz | |
Laser interface | IPG ZLR2) |
2) others upon request
Industrial PC and illumination unit
Industrial PC | Illumination unit | |||
---|---|---|---|---|
Size | 19", 4HU | Standard setup3) | 4 LED stripes, square setup | |
Weight | 10 kg | Wavelength | 850 nm2) | |
Mains | 100 - 240 VAC, 50/60 Hz | |||
Standard configuration | Windows 10, Intel Processor 3 GHz, 16 GB RAM, NVIDIA GPU, 512 GB SSD, RJ45 |
2) others upon request
3) other versions available (spot-, stripe- und ring light)
Others
Others | ||
---|---|---|
Software features | Local user interface and remote operation, stitching: high resolution imaging for large work fields; Click & Teach function; parameter variation via pen definiton; stand-alone mode via external trigger; control/status display of hardware; logging function | |
Options | External infrared camera | |
Certifications/Standards | CE, RoHS, EMC, EN 60825 |
Learn more about the JENvelt® system
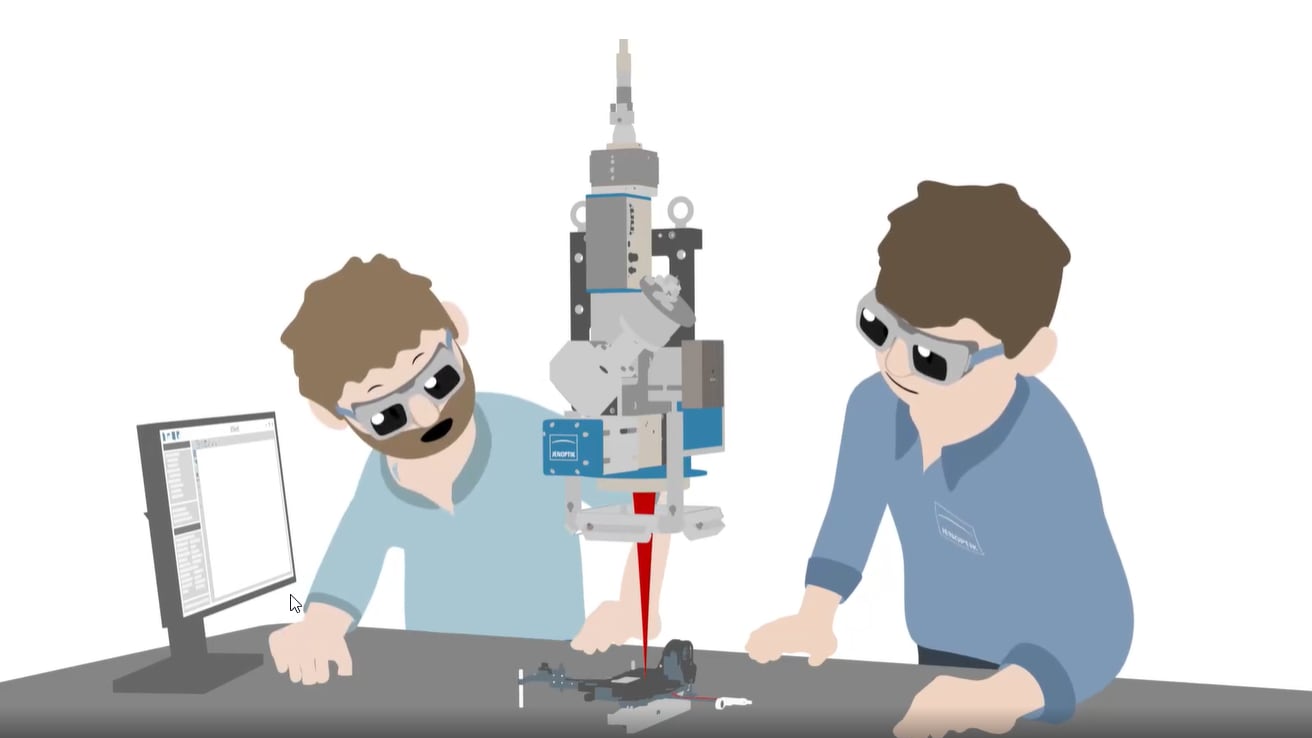
JENvelt® enables efficient multi-application-processing
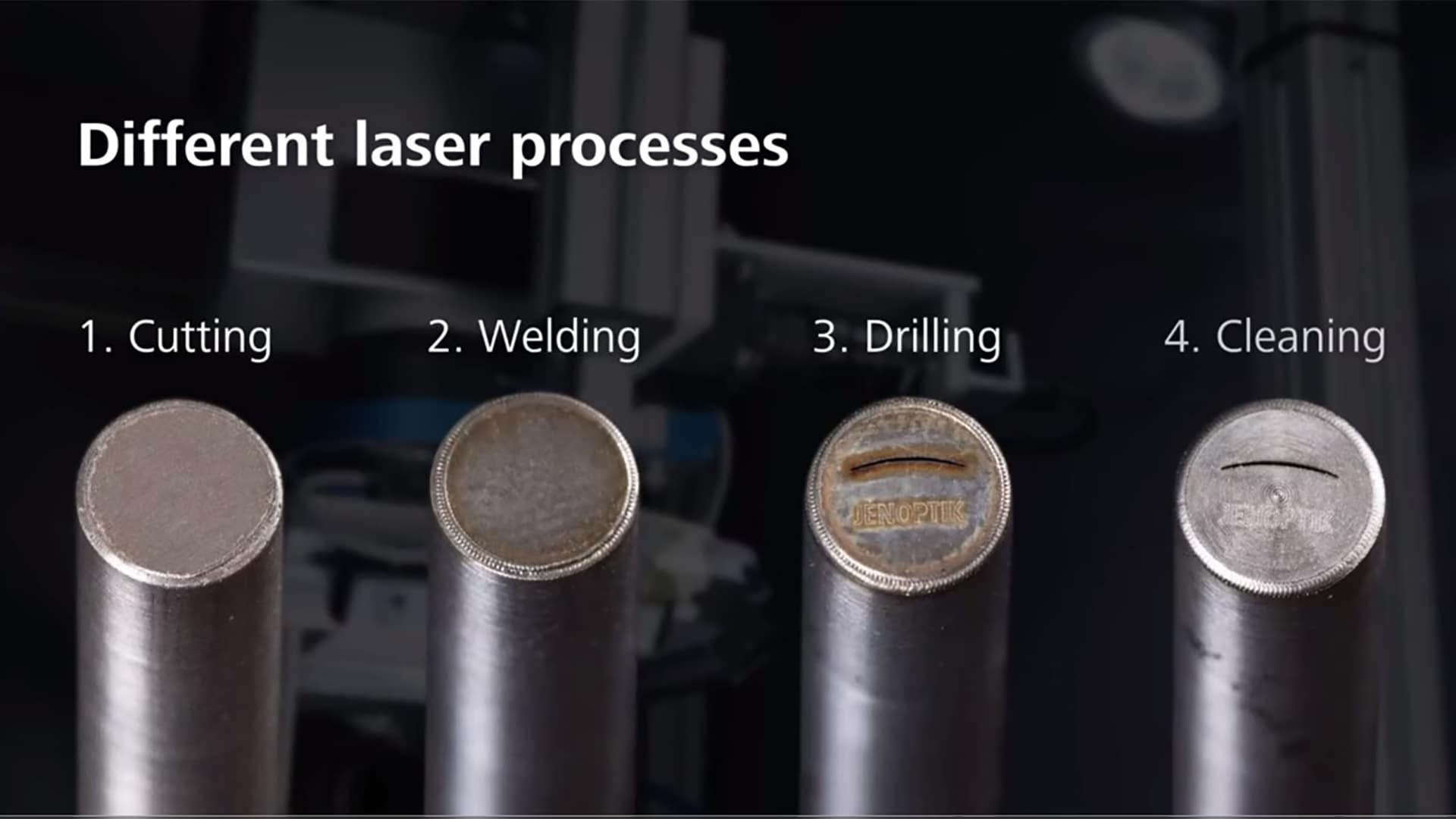
Steadily rising demands on quality and productivity in laser material processing increasingly require the integration of process monitoring systems in industrial material processing. Flexible solutions are in demand, which above all save laser machine manufacturers time and increase yield. To this end, JENOPTIK's JENvelt® vision-enhanced laser tool combines powerful optical components, such as F-Theta lens, beam expander or galvo scanner with integrated image processing and intelligent software in one system. The following video uses the example of an air nozzle to illustrate how different material processing tasks (cutting, welding, drilling and cleaning) can be implemented effectively and precisely with just one optical setup.
Real-time process monitoring is provided via the vision channel, which also allows adjustments to be made directly in the process if necessary. Extensive and exact component positioning is also not necessary, because the JENvelt® system uses software algorithms and image recognition to detect deviations in terms of position or component features and corrects them - for reliably precise laser results and a higher yield!
JENvelt® supports new process strategies for the automotive production
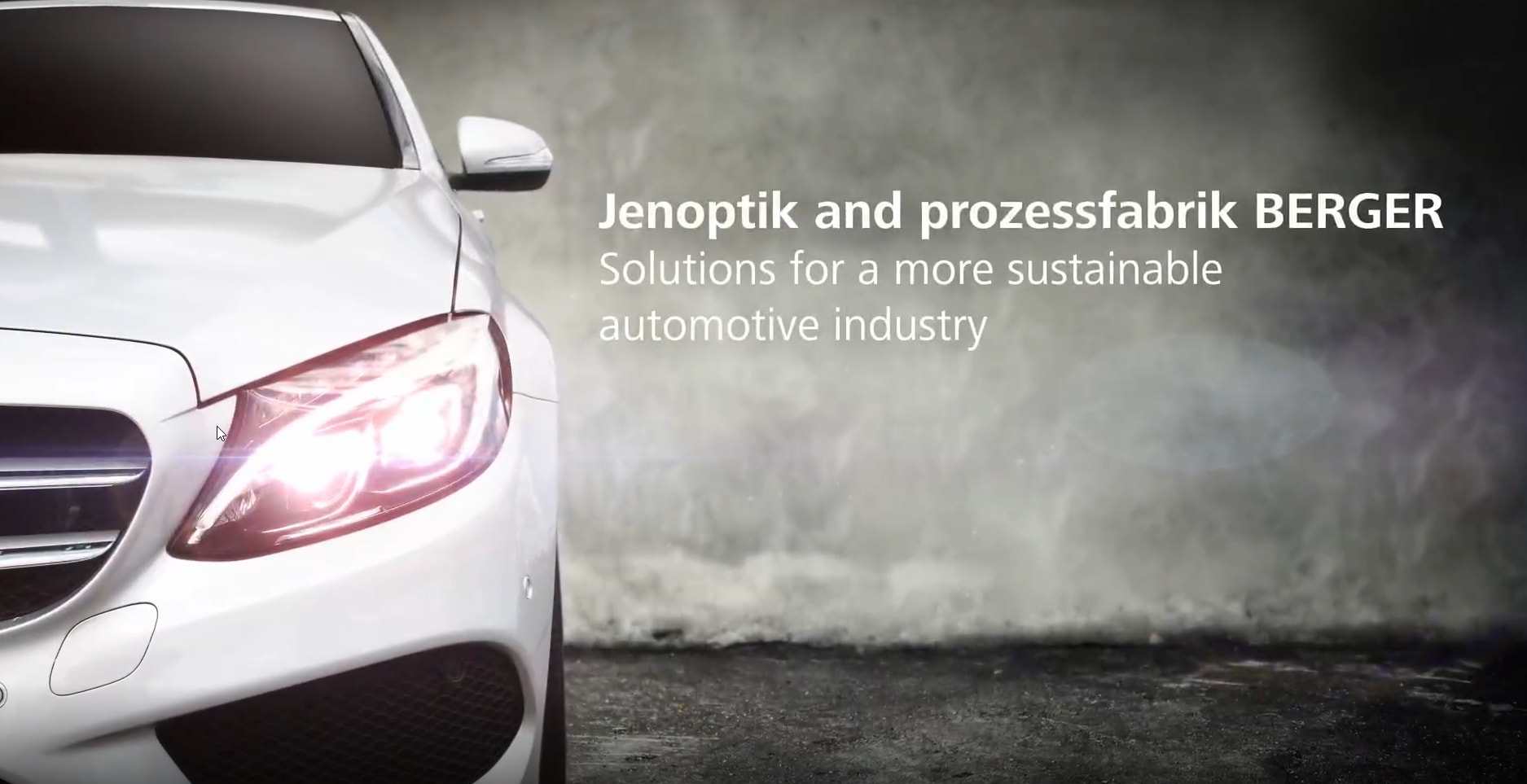
Re-use of defective parts
Take a glimpse into how the optical plug & play system JENvelt® helps to realize resource-saving production in the context of the automotive industry. The challenge in this video was to repair a complex component instead of disposing of it. In cooperation with the Berger process factory, a laser drilling process was developed that creates holes for later disassembly of an assembly using lasers.
JENvelt® not only provides reliable control and positioning of the laser for the drilling process through intelligent software, but it also allows for reliable quality control of results. This is all possible with just one ready-to-install system that can be integrated into laser machines.
Have any questions? Our experts can help!
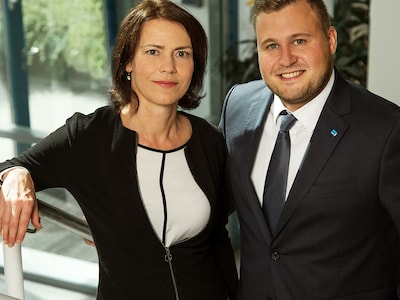